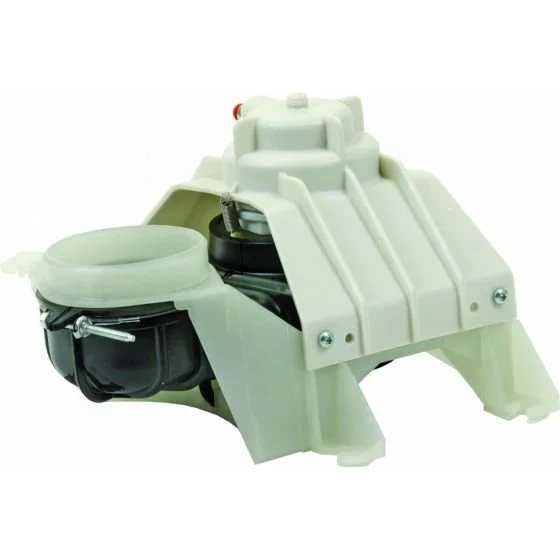
Whatever brand of commercial laundry equipment you have…we have the technician and parts to service it.
What you need to fix your commercial washer or dryer.
Arizona Commercial Laundry is great at service calls. We are also fast. We work on not only Wascomat and Electrolux machines but all brands such as: American Dryer, Cissell, Dexter, Huebsch, Milnor, and Speed Queen.
We carry a full inventory of Wascomat (Electrolux) parts. These include belts, water valves, drain valves, relays, and computers.
We also carry a wide variety of other brands’ parts.
Wascomat Washer Error Codes.
-
01. No water.
This fault code is generated by the programming CPU card.
When filling with water, the level specified by the wash program must be attained within a certain time. This time is normally set to 10 minutes but can vary depending on the type of machine and the software. If the filling time exceeds the maximum allowed filling time, fault code 01 will be displayed.
Long filling times can be caused by a blocked filler valve, defective filler valve, a break in the cable between the filler valve control board, defective valve control board, leaking level system, etc.
-
02. Door open.
This fault code is generated by the programming CPU card. The fault code can only arise during an on-going wash program.
This fault code will be displayed if the input for closed door signals that the door has been opened during an on-going wash program.
This can be caused by a bad or defective door lock, loose cable to door lock, problem with door lock edge connection.
-
03. Door lock fail.
This fault code is generated by the programming CPU card. The fault code can arise at program start. If the door lock doesn't lock within a certain time after program start, this fault code will be shown.
This fault code will also be displayed if the door lock for closed door signals that the door has been unlocked during an on-going wash program.
This can be caused by a bad or defective door lock, loose cable to door lock, problem with door lock edge connection.
-
04. NTC Low temp
This fault code is generated by the programming CPU card. This fault code is displayed if the temperature around the NTC sensor is below approx. -9 degrees C.
A low temperature means the resistance in the sensor is too high, above approx. 23.7 kohm. This can be because the machine has been standing outdoors, an open circuit in the sensor, a break in the cable to the sensor,
etc.
The resistance should be as shown in the table below:
Approximate values of a fault free temperature sensor
T (°C) R (ohm)
19 6100
20 5850
21 5600
22 5350
23 5100
-
05. NTC High temp
This fault code is generated by the programming CPU card. This fault code is displayed if the temperature around the NTC sensor exceeds +98 degrees C.
A high temperature means the resistance in the sensor is too low, lower than approx. 350 ohm. This can be caused by a short circuit in the sensor, break in the cable to the sensor, etc.
-
06. Water in machine
This fault code is generated by the programming CPU board. This fault code may appear only in the case of rapid advance to the end of the
program. The fault code will appear if the level system has not indicated “empty drum” within a certain time (approx. 3 min). This time may vary depending on the size of the machine.
Action:
• Check drain for dirt.
• Blow through the level hose and check that it is not blocked and does not contain any water.
• Check in the service program that the level control is working correctly.
• Adding too much detergent
-
07. Drum overfilled
This fault code is generated by the programming CPU board. The fault code arises if the drum has been filled with water above a predetermined level during an on-going wash program. It can be caused by a blocked level hose, drops of water in the level tube, defective filler valve, defective electronic filler control, etc.
Action:
• Blow through the level hose and check that it is not blocked and does not contain any water.
• Check in the service program that the level control is working correctly.
• Check using the service program that all the water valves are working correctly.
-
08. No heating.
This fault code is generated by the programming CPU board. The fault code means that the temperature is rising too slowly when heating is active. The limit for this fault code is normally set to a water temperature increase of approx. 3°C per 10 minutes but can vary depending on the type of machine and the software.
The fault code can be caused by a defective heater element, a break in the power supply to the heater element, defective heater contactor, etc.
On machines built for washing mops, it can be caused by too low a level in the program stage. The lowest level for a mop program in the main wash with heating is 90 scale units.
-
09. Drum overfilled
Only for coin machines.
This fault code is generated by the programming CPU card. The fault code is caused by the mechanical level control in the machine, by safety reason a doubled level system. The fault code arises if the drum has been filled with water above a level that normally should have generated fault code 07.
It can be caused by a blocked level hose, drops of water in the level tube, defective filler valve, defective electronic filler control, etc.
Action: see fault code 07.
-
10. Drum not drained
This fault code is generated by the programming CPU card. The fault code arises if the water in the drum is not below a predetermined level when a drain period has been completed in the wash program. It can be caused by a blocked drain, blocked level hose, a water drop in the level hose, defective level control, restricted drain lines to the machine, too many machines emptying simultaneously into drain pipes that are too narrow, etc.
Action:
• First check the drain installation and that the waste water can flow freely out from the machine without any restrictions.
• Check the drain valve in the machine with regard to dirt.
• Blow through the level hose and check that it is not blocked and does not contain any water.
• Check in the service program that the level control is working correctly.
-
11. UNB at program start
This fault code is generated by the programming CPU board. The fault code means that the mechanical imbalance breaker is already active when the wash program starts. It can be caused by a defective imbalance breaker, mechanical problem making the imbalance breaker always active, short in the edge connection or cables, etc.
-
12. Program failure
This fault code is generated by the programming CPU board. This fault code means that one of the CPU board memories can be defective.
Action:
• Try reloading the software into the machine memory. If this does not help, the CPU board will have to be replaced.
-
13. No motor comm
This fault code is generated by the programming CPU board. The fault code arises if the CPU board cannot communicate with motor control via the communication cable. Most likely this is the inverter has gone bad.
Actions:
• Check that there is power reaching the motor control.
• Then check that the indicator LED on the motor control is on. The LED
can be seen by looking down by the motor control edge connections.
• Check also that the communication cable between the CPU board and the motor control is intact and not damaged. Measure also with a reference instrument to see whether there is contact between all the leads in the communication cable.
-
14. Level adjust
This fault code is generated by the programming CPU board. The fault code arises if the circuit board’s internal level system has not been calibrated by the manufacturer.
-
15. Emergency Stop
This fault code is generated by the programming CPU board. The fault code arises if the emergency stop switch has been activated on the machine.
The cause can be inadvertent activation of the emergency stop, defective emergency stop switch, incorrect or shorted cable, etc.
-
17. Door lock
This fault code is generated by the programming CPU card. The fault code arises if the door lock is locked at the start of the wash program, i.e. that the door is locked although the CPU board has not requested locking. This fault code will be shown if one try to start a program when the DLCU has given a fault code.
-
18. Start not allowed
The machine’s program unit has been disabled by a superior monitoring system.
Actions
• Get in touch with the supplier of the monitoring system for possible causes of the monitoring system disabling operation of the wash machine.
-
19. Master comm.
Communication with superior system has been broken. The cause can be a fault in the network connections, damaged cable, defective monitoring system, etc.
Action:
• Firstly, contact the supplier of the monitoring system for possible causes of the monitoring system not communicating.
-
20. I/O MCU Interlock
This fault code is generated by the programming CPU board. The program controller has read from the motor control or I/O board that the interlock is not active. The reason for interlock failure can be a problem with the hatch lock, damaged motor supply cables or the I/O board with interlock voltage etc. The most probable fault source is the I/O board.
-
21. I/O Communication
This fault code is generated by the programming CPU board. The program unit cannot communicate any longer with one or more I/O boards in the machine that it has communicated with before. The cause can be a problem with the machine’s internal communication cables or that one or more I/O boards have lost their address.
Action:
• (Requires password) Check the machine’s internal communication
cables. Readdress all the I/O boards in the system using the service
program if the cables are not at fault.
Note.
If only one I/O-card in machine, press the service button on the I/O card about 10 seconds or until the LED goes out. Now I/O card 1 will be addressed as No. 1.
-
23. No I/O addressed
The fault code means that there is no I/O board addressed in the system at all.
Action:
• (Requires password) Readdress the existing I/O board from the service menu.
-
24. Checksum from DLCU
This fault code is generated by the programming CPU board. The program unit has detected a fault in the internal communication in the DLCU-processor.
Action:
• Replace the CPU board.
-
27. Level offset
This fault code is generated by the programming CPU board. The fault code arises if the level system indicates a level at the start of the wash program (when the drum should be empty) that exceeds what the program unit can compensate for automatically. This can be caused by blocked drain, blocked level hose, a drop of water in the level hose, leaking level system, defective level control, etc.
Action:
• Check drain for dirt.
• Blow through the level hose and check that it is not blocked and does not contain any water.
• Check in the service program that the level control is working correctly.
-
28. CPU/DLCU Low Levels
The DLCU contains a mechanical level monitor which ensures that there is no water in the machine when the lock opens. To ensure that the level monitor functions correctly, the mechanical level monitor is compared with a nominal value generated by the CPU, which is compared with the electronic level check.
When the water level exceeds the nominal value, a check is made to ensure that the mechanical level monitor is switched on, and if so, a fault code is generated.
Reason:
• The level controller can be damaged:
• Cross talk in the level controller electrical system.
• Leakage in the level controller’s air hoses.
• Incorrect nominal value, possibly caused by a fault in the electronic level controller.
Action:
• Check the level controller function. (Switch-on level = 40 mm, switch-off level = 15 mm Wg)
• Check the cables and their connections. The voltage across the level controller should be 0 V when the water level is < 15 mm Wg and 5 V when water level is > 40 mm Wg.
• Check that the level hoses are not blocked. Blow clean all the hoses in the level system.
-
31. Heat sink too hot
This fault code is generated by the motor control. There is a temperature sensor (NTC) mounted on the motor control cooling flange next to the power transistors in the output stage. If the temperature of the cooling flange gets too high (> 90°C) the fault code will be set to protect the transistors.
The cause of high cooling flange temperature can be e.g. a stiff drum in combination with intensive use and high ambient temperature. There may also be a fault in the motor (sticking bearings or short circuit in windings, which impairs the efficiency of the motor). There may also be a fault in the motor control temperature measuring circuits.
Actions:
• Make sure the drum turns easily.
• Check the value on the fault code counter for fault code 31.
• Check the last 8 motor control fault codes.
• Start a 90°C normal program with load on continuous operation and measure the temperature of the motor and motor control.
• Replace the defective part.
-
32. Motor too hot
This fault code is generated by the motor control. Each time the motor is started from stationary, the motor control will first measure the resistance between two phases in the motor. The motor control processor governs the output transistors so that a determined DC current flows between two phases in the motor winding. The actuation of the transistors is a measure of the voltage applied to the winding and the resistance can be calculated using the current and voltage values. The resistance can then be converted to a temperature since the winding resistance at 20°C and the temperature coefficient are known. If the average value of the four latest temperature readings is higher than the maximum motor temperature (e.g. 130°C), the ”Motor too hot” fault code will be activated.
The cause of high motor temperature can be a stiff drum, possibly in combination with intensive use and high ambient temperature. There may also be a fault in the motor (sticking bearings or short circuit in windings, which impairs the efficiency of the motor). There could also be a contact fault in the connectors between the motor control and the motor or a fault in the motor cable. A fault in motor control temperature measurement circuits can also occur.
Actions:
• Make sure the drum turns easily.
• Check the value on the fault code counter for fault code 32.
• Check the last 8 motor control fault codes.
• Measure the three phases to the phase resistors on the motor control motor connector (disconnect motor control and take the reading in the cable connector) to make sure they are the same.
• Start a 90°C normal program with load on continuous operation and measure the temperature of the motor and motor control.
• Replace the defective part.
-
33. No interlock
This fault code is generated by the motor control. The motor control must be powered with 230V/50 Hz on the interlock input in order to drive the motor. This signal is confirmation that the door is closed and locked. Motor control receives its commands to rotate the drum from the timer via a serial communication link between the motor control and timer. Since the timer also has access to the interlock signal, the timer must never send a run command to the motor control if the interlock signal is missing. If this does happen, the ”No interlock” fault code will be activated.
The cause of this fault code being activated can be e.g. a break in the cable leading the interlock signal to the motor control. There may also be a fault in the connector in the door lock, which connects 230V/50Hz to the interlock signal. A fault in the interlock circuits of the motor control can also set this fault code.
Actions:
• Use a measuring instrument to check that the interlock signal comes on X302:1-2 when the door lock is activated. Read also bit 1 in the second
bye under ”Motor Status” in the service program (the bits are numbered from 0 to 7 where bit 0 is on the far right). If bit 1 in the second byte is 1 then the lock is open, while a 0 indicates that the lock is closed.
• Replace the defective part when it has been located.
-
35. Motor short circuit
This fault code is generated by the motor control. The motor control reads the power consumption of the motor continuously. If the current for some reason gets too high (= exceeds a certain limit), the motor control will cut the current to the motor. After the motor has stopped (= tachometer indicates stationary motor), the motor control will attempt to restart it. If the motor control then detects high motor current again, the ”Short circuit motor” fault code will be activated. If on restarting after a first short circuit, the motor control rotates normally, a fault code will not be activated.
This fault code can be activated for a number of reasons:
• Short circuit in motor
• Short circuit internally in motor winding (impaired efficiency, higher current consumption)
• Short circuit in motor cables
• Short circuit in connectors
• Drops of water causing short circuits in the motor connector
• Short circuit in the motor control output transistors
• Bad contact in tacho signal
• Bad contact in interlock signal
Actions:
If the fault is a stable one, it is generally not difficult to locate the defective unit through resistance measurement and testing with the service program.
Further information can be obtained by studying the contents of ”MCU
FAULT LOGGER”. Study the following:
• SHORT CIRCUIT 2 (specifies how many times fault code 35 has been
active)
• SHORT CIRCUIT 1 (specifies how many times the current limit has been exceeded. The difference between short circuit 1 and short circuit 2 indicates how many times there has been a short circuit 1 that has not been confirmed when restarting the motor).
• LAST FAULT CODE N/8 (shows the 8 latest fault codes)
• TACHO CUT-OUT LOW RPM (can give a clue in case of intermittent faults)
• TACHO CUT-OUT HIGH RPM (can give a clue in case of intermittent faults)